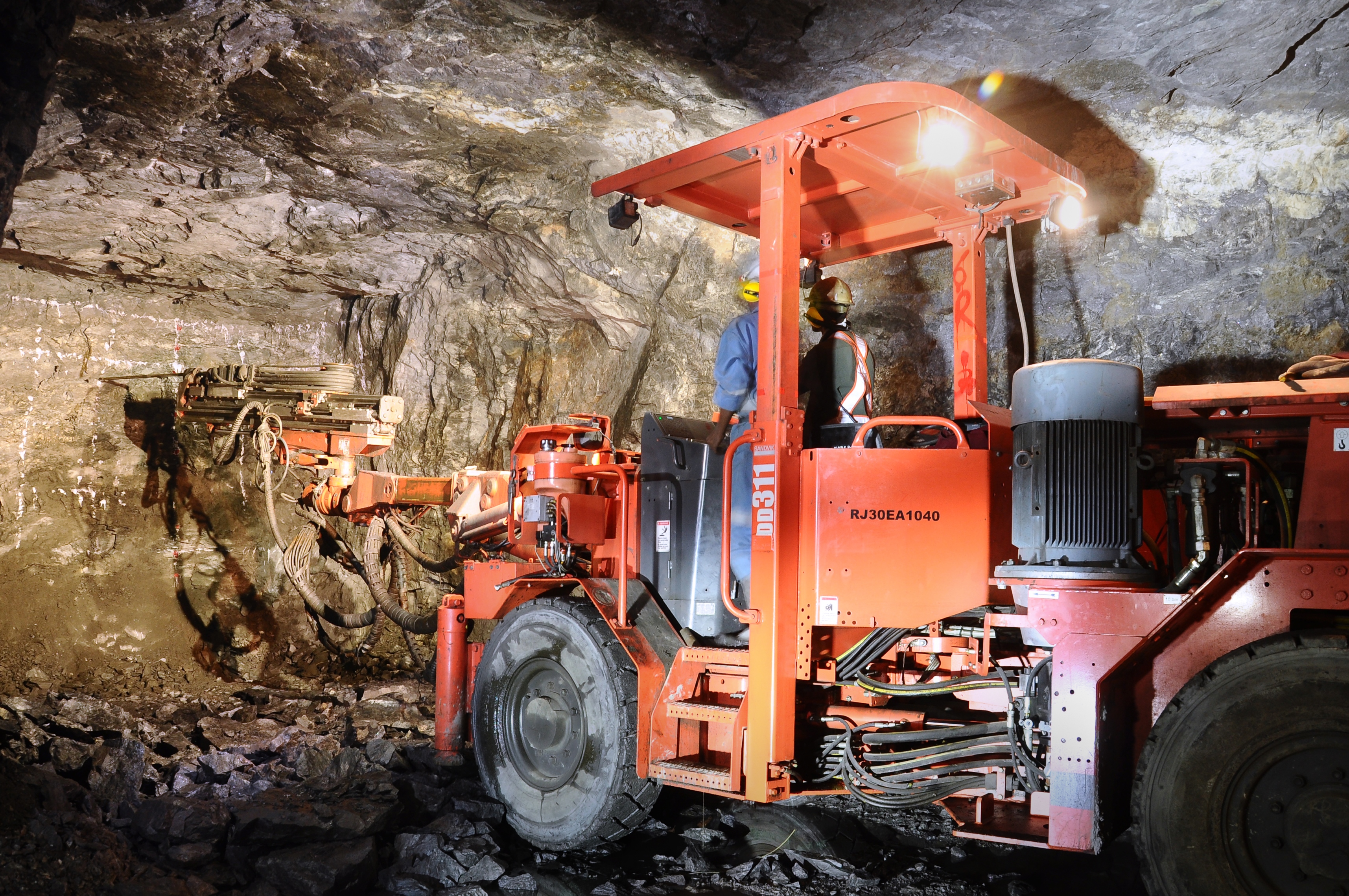
FINANCIAL CHRONICLE
By Sunil Duggal, CEO of Hindustan Zinc & President of FIMI
Wednesday, 3 October 2018
The development of natural resources dates back to about 50,000 years – in the Middle Paleolithic Chert mines of Nazlet Sabaha (or Safaha), a site on the western banks of the Nile River in Egypt. In India, zinc mining dates back to over 3,000 years in Rajasthan at Zawar.
Mining was important in the ancient times and it is important today for the survival of mankind. Development of natural resources is essential for sustaining economies. But this is one of the most misunderstood sectors in terms of care for the environment and sustainability. But one needs to understand that you need metals for the growth and prosperity of nation and also for the benefit of mankind.
Above the earth is agriculture and below the earth are minerals. Only if minerals could be sown, mining would not have been needed. The development in technology, innovation and sophisticated machines has given new definition to the mining industry. It’ not just mining today, it is mining with data mining.
The concept of safe mining has become larger than volumes and profits. Mining firms are more inclined towards developing green belts, create jobs and make operations more sustainable. Mine digitisation has developed intelligent mines that are smart, connected, wired and analytical. Digitisation also helps in making data-driven decisions. The value derived from existing assets gets maximised with greater precision and transparency. It is ultimately making mining better, faster and safer along with other benefits. Technologies like real time monitoring, advanced sensor and analytics are helping in optimisation, cost reduction and increase in efficiency.
With digitisation, it’s possible to build algorithms all the way from exploration to metal production. Predictive algorithms enhance precision, speed of maintenance and metallurgy. It has also improved management of energy and water resources and emissions. With ease of predictability, there is better preparedness and cost optimisation. Digitisation has also helped integration of processes to create one ultimate platform where different departments like sustainability, safety, production, cost and HR are visible. It has certainly changed the dynamics in the mining industry.
With digitalisation-enabled systems, many global firms have a ‘life of mine’ concept. Few have started driverless haulage that are equipped with a GPS, an obstacle detection system and vehicle controllers. These unmanned trucks increase mine safety, lower the operating costs and reduce wear & tear on tyres. The world is exploring the movement of vehicles through remotes – the objective is to avoid man and machine collusion.
Indian mining firms are not far behind. Besides adopting the latest technology, there are many startups that are developing innovative technology to raise efficiency bringing minimum harm to the environment. When HZL, the only Indian firm that produces integrated zinc-led-silver, carried out its first aerial survey over a decade ago to locate mineral resources in Rajasthan, it attracted hundreds of villagers.
The company is developing intelligent mines that would be smart, connected, safer and more productive. In exploration, it is using remote sensing technologies. The experts are now moving on to implement an automated core scanning technology. A highly sensitive technology, this can also project the rock and terrain properties along with the content of the ore.
Other technologies that are being integrated by it include adopting augmented and virtual reality wearables and ore body intelligence that will help in higher predictability. Ore body intelligence enables geo-metallurgical characterisation faster, cheaper and in a more integrated manner. As soon as drilling is done, minerals present will be known, without waiting for 3-6 months.
3D laser scanning is another such technique being adopted by Hindustan Zinc, which will eliminate the need for experts to physically visit the mine. It would save time and money. This technology can map the shape, position and location of objects with high precision, allowing mining firms to accurately plan and prepare for exploration and drilling.
The transport management system, comprising processes like sequencing, route defining, geo-fencing, weighing and billing are also being automated. The introduction of high speed Wi-Fi networks in underground mines, high bandwidth optical fibre, voice over internet protocol (VoIP) and other IP-based devices will enable surface control of man, machine and materials at each level of the mine and improve stope enhancing productivity, underground traffic management and safety, along with ease in asset tracking, data transfer, real time equipment health monitoring.
HZL is also aiming to develop an integrated analytics & operations collaboration centre in Udaipur in 2-3 years. Thus, all data on output from mines, mills, smelters, power plants will be analysed at one place and results and feedback will be sent to the operations department, which will plan future actions to optimise operations.
Further, with digitisation, the entire value chain will be enhanced right from beneficiation to smelting to green power to waste management. HZL’s silver-rich Sindesar Khurd mine in Rajasthan has turned out to be one of the most mechanised and digitised mines in the world. The firm is looking to convert 80 per cent of the fleet of vehicles in Sindesar Khurd mine into autonomous in 3 years and conduct operations like autonomous drilling and haulage, remote controlled operations, real-time asset tracking and monitoring.
With technology adoption and innovations, HZL has been successful in enhancing exploration. Latest 3D modelling software has been enabled for better visualisation of ore bodies, which has helped in identifying drilling gaps and the hidden ore. It has also been conducting trials of ‘big data’ machine to identify new target areas at its Rajpura Dariba mine in Rajasthan. It would help in exploration and extending mine life. Technology is extensively used for ore fragmentation, sorting and slurry pumping which has helped in improving recovery from tailings. It has also introduced technologies like cavity monitoring systems, mobile carrier rigs, V30 slot machines and refuge chambers for the first time in India.
India produces 87 minerals, which include 4 fuel minerals, 10 metallic minerals, 47 non-metallic minerals, 3 atomic minerals and 23 minor minerals. Why be an importer of a mineral that can be exported in abundance. Why create jobs in other countries, when our own youth are unemployed. Why pay hefty import bills, when India has the strength and resources to gain tremendously through exports.
There are some nations that are blessed with mineral resources and there some who would always want to be in leadership position towards mineral production. India is one such country that has been blessed with both.